Precise filtration device for pyrolysis reactor
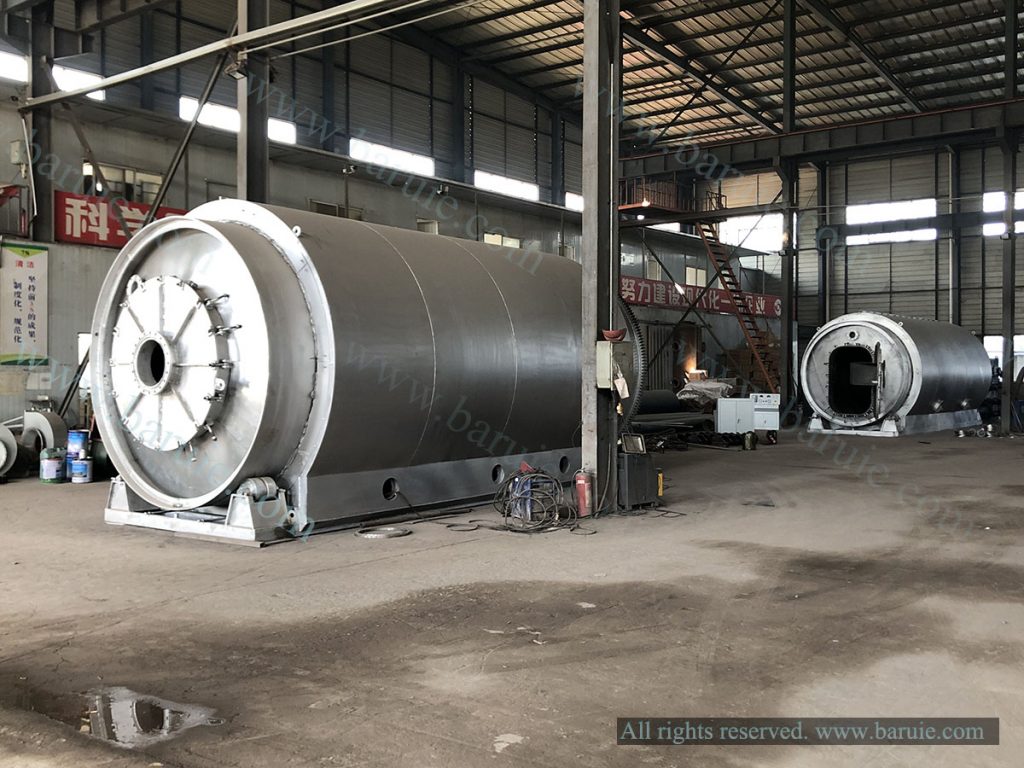
At present, the solid waste pyrolysis reactor outlet filter structure is too simple, it is difficult to continuously and stably produce gas in the pyrolysis reactor, and also affects the quality of the pyrolysis gas, resulting in a large number of flue gas entrained with solid particles, which reduces the cracking efficiency. In serious cases, it accumulates in the reactor door and causes blockage, so that the pressure in the pyrolysis reactor is too high and explosion occurs. That affects its safety operation.
In order to avoid the shortcomings of the existing technology, our company provides a new type of filtration system for the pyrolysis reactor of organic solid waste. When the organic solid waste is cracked, it can effectively prevent the large solid particles from being taken away by the gas, maintain the relatively stable pressure in the pyrolysis reactor, make the continuous and stable gas production in the pyrolysis reactor, and improve the quality and cracking efficiency of pyrolysis gas 。
The new filtering system is characterized in that: the mesh blocking plate, the arc-shaped barrier cover, the air outlet cylinder, the object blocking cylinder and the fixed support are included, wherein: the air outlet cylinder is cylindrical, which is arranged at one end of the pyrolysis reactor and connected with the inside and outside of the pyrolysis reactor; the object blocking cylinder is cylindrical in shape, and its diameter is larger than that of the air outlet cylinder, and is sheathed on the outer circumference of the gas outlet cylinder; one end of the barrier cylinder is fixed on the inner furnace wall of the pyrolysis reactor; and The other end of the object cylinder is connected with the mesh blocking plate;
The mesh baffle is cylindrical with one end open and the other end closed, and the end of one end of the opening is sealed and connected with the end of the object blocking cylinder; The arc-shaped barrier cover is arranged on the inner side of the mesh blocking plate, including an arc-shaped part and a cylinder part, the outer diameter of the cylinder part is smaller than the inner diameter of the object cylinder; the inner diameter of the cylinder part is larger than the outer diameter of the air outlet cylinder, and there is a certain length of interlacing between the end of the cylinder part and the end of the object blocking cylinder, so as to make the inner wall of the barrier cylinder and the outer wall of the cylinder part, as well as the inner wall of the cylinder part and the air outlet cylinder A 180 degree U-shaped outlet port is formed between the outer walls;
A fixed bracket is arranged between the outer wall of the cylinder part of the arc-shaped blocking cover and the inner wall of the object blocking cylinder, so that the arc-shaped blocking cover is fixed on the object blocking cylinder.
The other end of the barrier cylinder is connected with the mesh blocking plate, and the connection mode is preferably threaded connection.
The small hole shape of the mesh blocking plate can be circular, elliptical or square.
The small hole of the mesh blocking plate is preferably circular, with a diameter of 18-22mm.
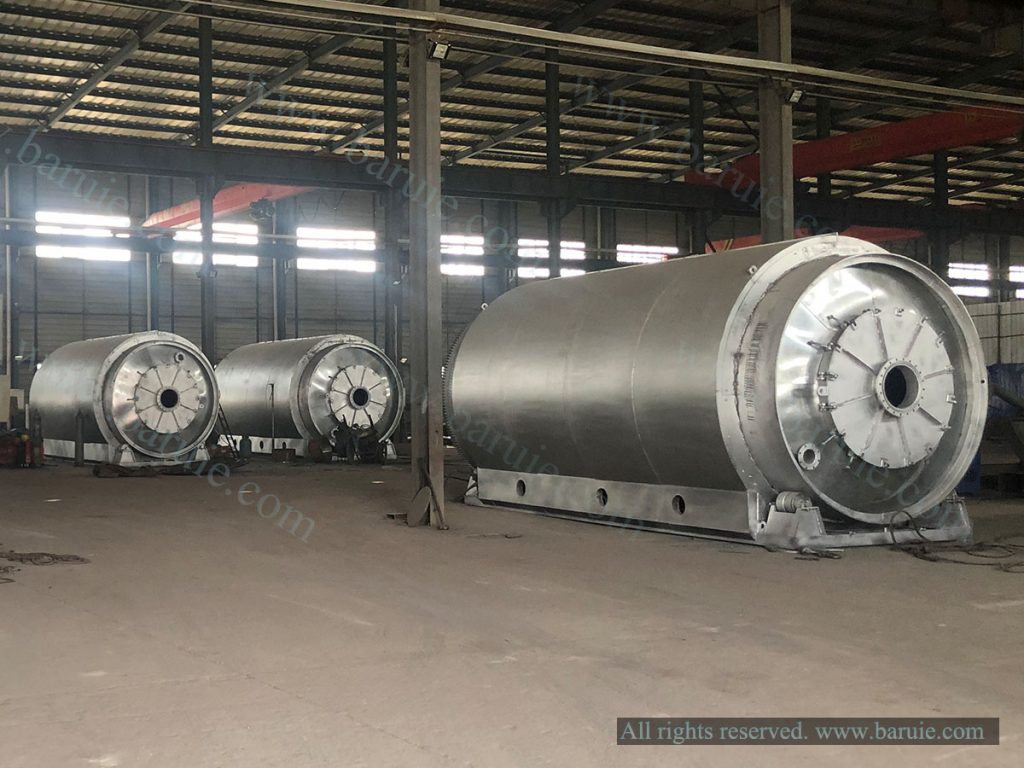
The advantages of our patented technology are as follows: The pyrolysis of organic solid waste produces pyrolysis gas and large incompletely cracked solid particles, which move towards the gas outlet. When the larger solid particles meet the mesh barrier plate, they are stopped for further thermal cracking. The barrier cylinder connected with the mesh barrier plate prevents the un-cracked solid particles from approaching the outlet port, and the smaller particles and gases continue to move along the outlet port. The small solid particles stick on the air stop cylinder and continue to crack when heated, and the gas is discharged through the outlet port. The defects of furnace door blockage and low cracking efficiency caused by incomplete cracking in the prior art are avoided.