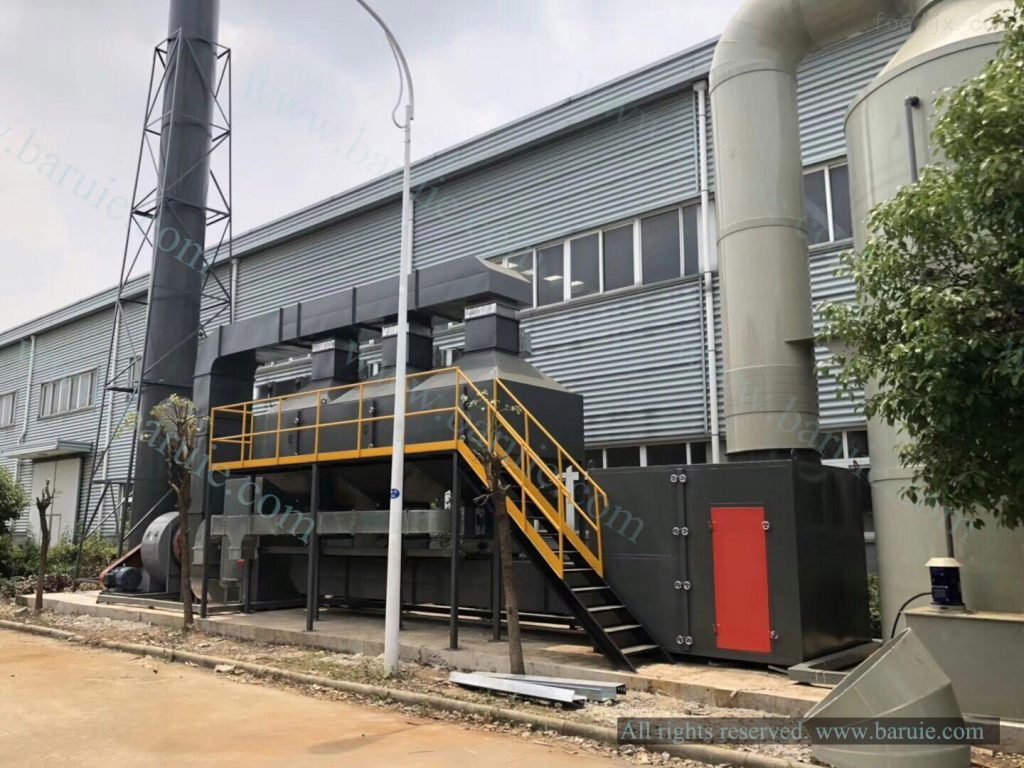
- Commodity: workshop exhaust gas treatment engineering design and construction
- Specification: 10,000 to 100,000 m3/h
- Gas resources: chemical industry plants, oil refineries, painting workshops, flue gases, and so on.
- Work theory: catalytic burning oxidization
- Catalysts type: structure precious meta catalysts
- End products: CO2 and H2O
- Warranty period: 1 year
- Design working life: 15 years
Introduction to the process principle
The main components of the exhaust gas are benzene, toluene, xylene, non-methane hydrocarbons, styrene, butadiene, acrylic acid, styrene-butadiene rubber, acrylene acrylate, and other volatile and harmful gases such as VOCs.
Volatile organic compounds (VOCs) are a class of highly toxic and seriously polluting chemical substances. At present, the pollution problem of VOCs is increasingly being paid great attention by various countries, and China has promulgated the Comprehensive Emission Standards for Air Pollutants, which stipulates strict emission standards for various types of organic pollutants in the air. Domestic and foreign VOCs pollution control methods currently include adsorption, absorption, biological treatment technology, membrane separation technology, direct combustion, catalytic combustion method. Among them, the catalytic combustion method is an efficient and clean combustion technology, which mainly utilizes catalysts to make organic waste gas fully combusted under lower temperature conditions. Relative to other treatment technologies, catalytic combustion has significant advantages: low ignition temperature, low energy consumption, high processing efficiency, no secondary pollution, etc., making it one of the promising VOCs organic waste gas treatment methods. High-efficiency catalytic combustion catalyst is the key core of catalytic combustion technology, and the catalyst with block carrier as the skeleton matrix is called regular structure catalyst, also known as integral catalyst. Due to the special pore structure, this type of catalyst improves the material transfer on the catalytic reaction bed, improves the catalytic efficiency, lowers the pressure, and reduces the operation cost, which is more and more widely used in multi-phase catalytic reaction of petrochemicals, fine chemicals, and so on.
Catalytic purification is a typical gas-solid phase catalytic reaction, the essence of which is the deep oxidation with the participation of active oxygen. In the process of catalytic purification, the role of catalyst is to reduce the activation energy, while the catalyst surface has adsorption, so that the reactant molecules enriched in the surface to improve the reaction rate, accelerate the reaction; with the help of catalyst can make organic waste gas in the lower ignition temperature conditions, flame-less combustion and oxidative decomposition of CO2 and H2O, and at the same time, a large amount of thermal energy, so as to achieve the removal of harmful substances in the waste gas. The method of catalytic purification.
In the process of catalytic purification of the exhaust gas, the exhaust gas is fed into the heat exchanger through the pipeline by the fan, and the exhaust gas is heated to the starting temperature required for catalytic combustion.
The preheated exhaust gas passes through the catalyst layer and burns. Due to the role of the catalyst, the catalytic combustion method of exhaust gas combustion of the starting temperature of about 250 to 300 degrees Celsius, much lower than the direct combustion method of combustion temperature of 650 to 800 degrees Celsius, high temperature gas into the heat exchanger again, cooled by the heat exchange, and ultimately at a lower temperature by the fan discharged into the atmosphere.
Delivery List
- Activated carbon tower
- stainless steel spray scrubbing tower
- catalytic burning chamber
- Maintenance platform
- PLC electric control cabinet
- Frequency converter
- Electrical components
- Activated carbon
- Thermocouple
- Air damper
- Pressure sensor
- Pneumatic air damper actuator
- Fresh air fan
- De-sorption fan
- Main fan
- Catalysts
- Air duct
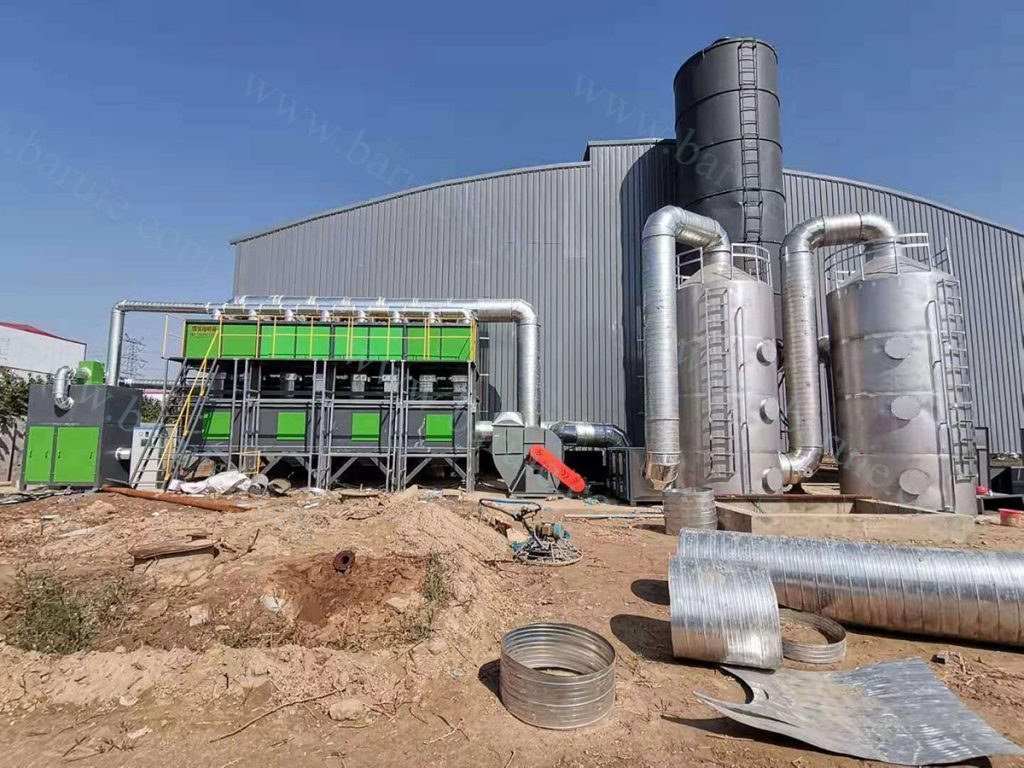
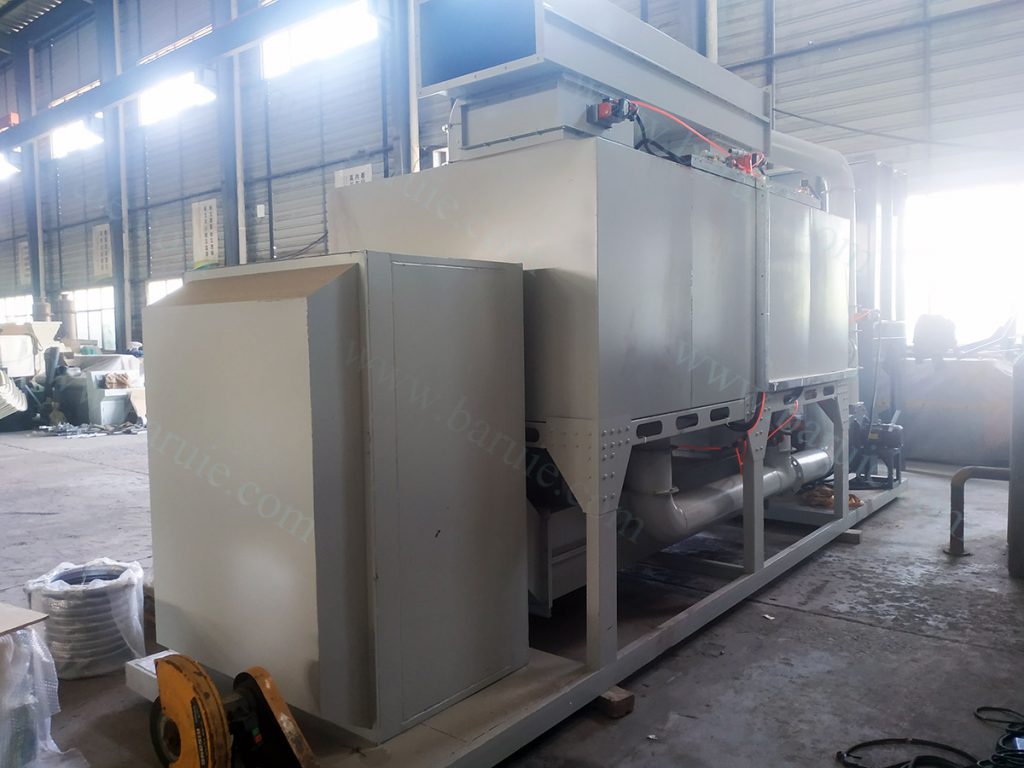